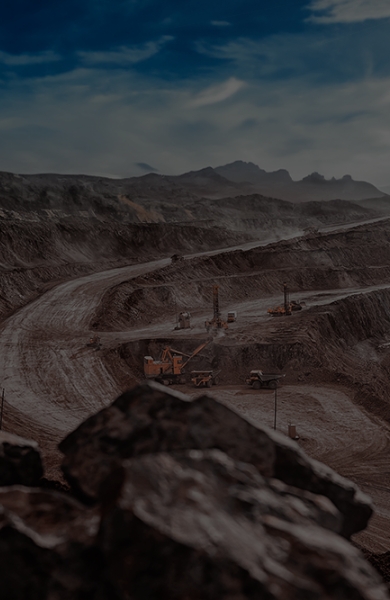
From Ore to Innovations:
Understanding the Copper Journey
The Dynamics of
the Copper Value Chain
Did you know that 75% of the world's copper mining takes place in just 10 countries, such as Chile, Peru, the Democratic Republic of Congo, and Indonesia? Interestingly, India's Hindustan Copper Limited contributes to 3-5% of the country's copper consumption. Below is a brief breakdown of how copper is integrated into our everyday routines.

Exploration and mining
The copper value chain begins with exploration to identify potential copper deposits. Once an economic deposit is found, mining operations are established. Copper mining occurs from open pits and underground mines, with the copper content in the ore bodies ranging typically from 0.5% to 1.5%.

Ore processing
The extracted pyritic copper ore is processed to remove impurities and increase its concentration. This involves crushing, grinding of copper ore and mixing it with water to form a slurry. Chemical reagents and frother are added, and the slurry is introduced into floatation cells. Rising air bubbles capture pyrites of copper particles, forming a layer collected in troughs. The condensed bubbles yield copper concentrate with typically 25%-50% copper content.

Smelting
Beneficiation of copper ores produces concentrates consisting mostly of sulphide minerals, with small amounts of gangue oxides. This material is oxidised to remove sulphur, iron, and silica to enrich copper grade typically to 64% to produce copper matte. The processes contain concentrate treatment in furnace followed by rotary holding furnace where the iron oxide and silica will be separated as slag. The matte is sent to converters to further remove sulphur and then to anode furnace followed by casting facilities to enrich copper concentration to 99.4 to 99.5% levels. The gas generated during smelting will be filtered to remove dust particles and pure gas will be converted into sulfuric acid.

Refining
The electro refining works on corrosion concept. The impure copper is placed as anode and a mother blanks is placed as a cathode. The electrolyte used is copper sulfate solution. When current is passed through the electrolyte pure copper content from the anode dissolves into the electrolyte, and the same amount of copper is deposited on the cathode having purity of around 99.99%. The purity is necessary to obtain the required electrical conductivity for electrical applications.

Fabrication
The refined copper cathode is then shaped into various forms, such as rods, sheets, tubes or wires, through processes like casting, rolling, and extrusion. These forms are mostly used as raw materials for further manufacturing of consumer goods or in some cases as end products.

Exploration and mining
The copper value chain begins with exploration to identify potential copper deposits. Once an economic deposit is found, mining operations are established. Copper mining occurs from open pits and underground mines, with the copper content in the ore bodies ranging typically from 0.5% to 1.5%.

Ore processing
The extracted pyritic copper ore is processed to remove impurities and increase its concentration. This involves crushing, grinding of copper ore and mixing it with water to form a slurry. Chemical reagents and frother are added, and the slurry is introduced into floatation cells. Rising air bubbles capture pyrites of copper particles, forming a layer collected in troughs. The condensed bubbles yield copper concentrate with typically 25%-50% copper content.

Smelting
Beneficiation of copper ores produces concentrates consisting mostly of sulphide minerals, with small amounts of gangue oxides. This material is oxidised to remove sulphur, iron, and silica to enrich copper grade typically to 64% to produce copper matte. The processes contain concentrate treatment in furnace followed by rotary holding furnace where the iron oxide and silica will be separated as slag. The matte is sent to converters to further remove sulphur and then to anode furnace followed by casting facilities to enrich copper concentration to 99.4 to 99.5% levels. The gas generated during smelting will be filtered to remove dust particles and pure gas will be converted into sulfuric acid.

Refining
The electro refining works on corrosion concept. The impure copper is placed as anode and a mother blanks is placed as a cathode. The electrolyte used is copper sulfate solution. When current is passed through the electrolyte pure copper content from the anode dissolves into the electrolyte, and the same amount of copper is deposited on the cathode having purity of around 99.99%. The purity is necessary to obtain the required electrical conductivity for electrical applications.

Fabrication
The refined copper cathode is then shaped into various forms, such as rods, sheets, tubes or wires, through processes like casting, rolling, and extrusion. These forms are mostly used as raw materials for further manufacturing of consumer goods or in some cases as end products.

Exploration and mining
The copper value chain begins with exploration to identify potential copper deposits. Once an economic deposit is found, mining operations are established. Copper mining occurs from open pits and underground mines, with the copper content in the ore bodies ranging typically from 0.5% to 1.5%.

Ore processing
The extracted pyritic copper ore is processed to remove impurities and increase its concentration. This involves crushing, grinding of copper ore and mixing it with water to form a slurry. Chemical reagents and frother are added, and the slurry is introduced into floatation cells. Rising air bubbles capture pyrites of copper particles, forming a layer collected in troughs. The condensed bubbles yield copper concentrate with typically 25%-50% copper content.

Smelting
Beneficiation of copper ores produces concentrates consisting mostly of sulphide minerals, with small amounts of gangue oxides. This material is oxidised to remove sulphur, iron, and silica to enrich copper grade typically to 64% to produce copper matte. The processes contain concentrate treatment in furnace followed by rotary holding furnace where the iron oxide and silica will be separated as slag. The matte is sent to converters to further remove sulphur and then to anode furnace followed by casting facilities to enrich copper concentration to 99.4 to 99.5% levels. The gas generated during smelting will be filtered to remove dust particles and pure gas will be converted into sulfuric acid.

Refining
The electro refining works on corrosion concept. The impure copper is placed as anode and a mother blanks is placed as a cathode. The electrolyte used is copper sulfate solution. When current is passed through the electrolyte pure copper content from the anode dissolves into the electrolyte, and the same amount of copper is deposited on the cathode having purity of around 99.99%. The purity is necessary to obtain the required electrical conductivity for electrical applications.

Fabrication
The refined copper cathode is then shaped into various forms, such as rods, sheets, tubes or wires, through processes like casting, rolling, and extrusion. These forms are mostly used as raw materials for further manufacturing of consumer goods or in some cases as end products.
NOTE: Copper is highly recyclable. Scrap copper from discarded products or manufacturing waste is collected, processed, and reintroduced into the value chain through smelting and refining. The mentioned above subject is process outline, which is proven technology across the globe. The detailed financials like capital investment, working capital and profitability to be worked out.